modern rustic dining room
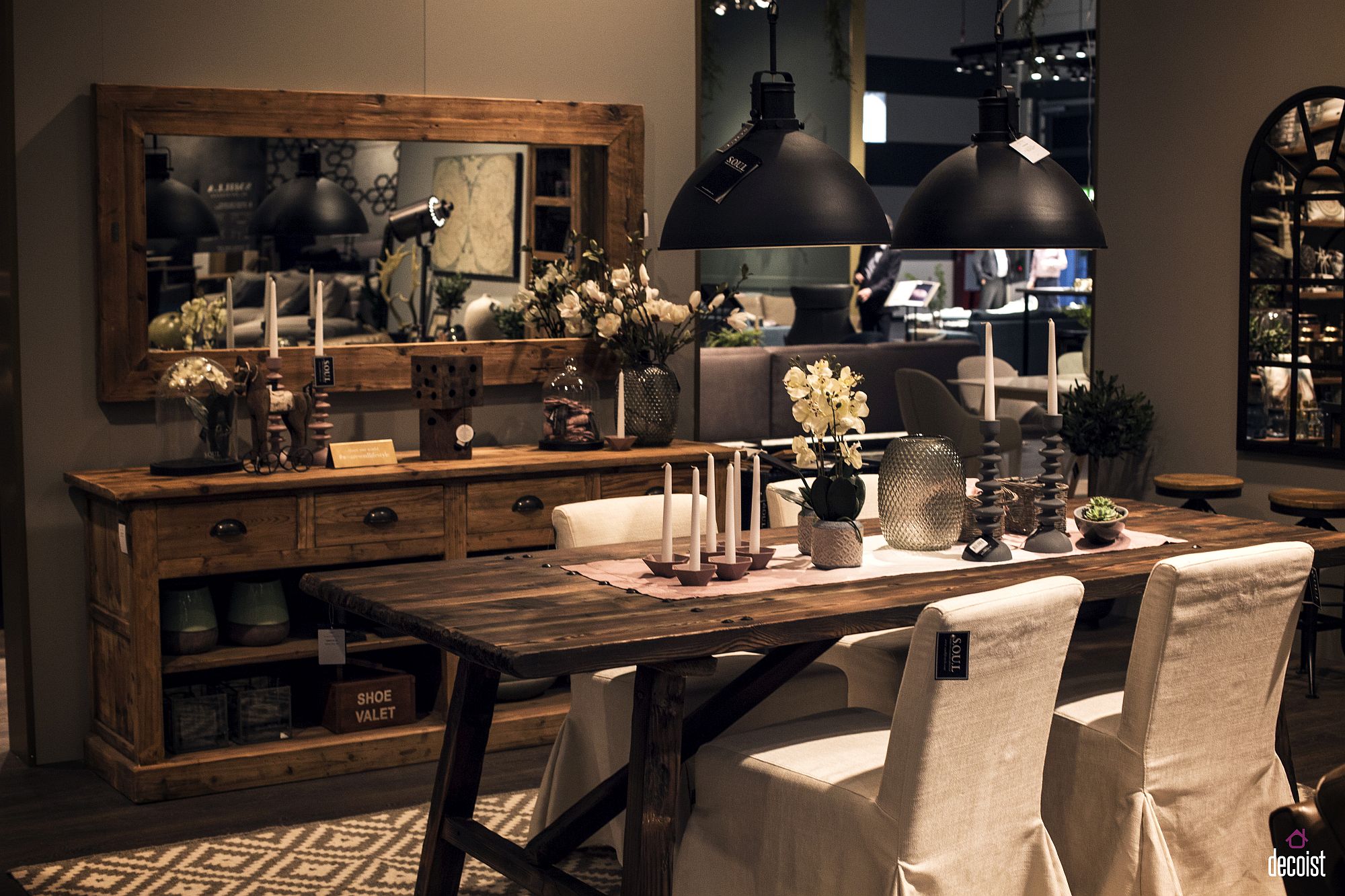
today i'm continuing my dining table buildand i've already made the dining table top if you haven't seen this and areinterested in this i'll post a link in the description belowwhere you can check out that video. but this dining table isn't going to be huge,this tabletop is about 27 inches by 62, which is small for most people, however it's perfectly sized for ourapplication in our house. it'll sit a maximum of four peoplewhich is exactly what we want. anyway i'm going to startwith the base on this, this slab of hickory this is a 3 inch thick slab of hickory,
that i got from my local woodworkingfriend of mine sean stone. and it's, it's got too much twist in it for me to makea actual slab top project out of it. so i think i'd be removing toomuch material if i try to flatten this, it'll just be wasteful. so, instead, i'm going to use this for the legs. this is enough material over here forone, two, three, four, all four of the legs, on this side of the slab,
and i'll have a lot left overto work with, as needed. but i can't put this through myband saw or table saw as it is, it's just too heavy and awkwardfor me to move around, so i think i'm gonna take it outside andrough cut it with a circular saw first. the maximum depth of thecircular saw is not enough to cut the slab all the waythrough so i have to finish the cutwith a reciprocating saw. then once back in the shopthe slab can be cut in half, to make the pieces a littlebit more manageable,
and then rough cut at the bandsaw. once these pieces are rough cut they canbe squared on two sides at the jointer, and then typically i would use my planer toget the other two sides square and parallel but instead i wanted to usemy table saw for this. i think it'd be a lot less stresson my planer blades because this material is so hard. unfortunately, because i'm using the table saw and onlytaking just a little bit off of one side of each one of these boards,
it's throwing dust everywhere, so, that's the only downside ofusing this particular method. at this point the legs are notdown to their final size just yet, they're a little bit oversized and this isbecause i want these to sit overnight and release any type of stressesthat they may have. the slab has been sitting for quite some timeand just cutting it up you may end up having a little bit of stress or movement. and i want to be able to mill that back outif there's any movement at this stage. i went ahead and redid the entire millingprocess once more after letting this sit,
and nothing moved,so we're good to go. these legs have quite a bit more characterin them than what i thought they would have. there's a lot of bug holesand defects here and there, so this is either going to look really nicebecause it's going to accent the table, or it's going to look reallycrappy, time will tell. but anyway i'm ready to start in on theapron rails and the mortises for those. now i've decided, my wife and i have decided that the basedesigns that i've come up with are just just too busy for the area that we have.
so instead of making a complicatedmultiple part base for this table, we're just going to go ahead and gowith a traditional four-legged base and then add some accents near the end. but right now i need to cutthe mortises for the apron rails and to do that i'm using a plunge routerand an edge guide attachment. real quick i want to mention thegrain selection for these legs. typically it's sought after to have quartersawn material for just about everything not so much in legs though. quarter sawn materials where the grain ispretty much vertical or very close to it,
so that on the top and bottom surfaces youhave a nice straight grain appearance. that's something that's reallynice on -say- like a tabletop. not so much on these legs because quarter-sawn material is nice and straighton one end but then on the other side it's basically like flat sawn material so it'slike that you have that cathedral look, which looks completely differentthan the straight grain looks. so, here, with the grain is somewhatof a 45 degree angle, then that means the grain iscoming through the side faces,
just about the same way on allfour of these sides resulting in somewhat more uniform straightgrain appearance on all four sides. in the end this will look a lotmore uniform all the way around than choosing something likethis which is quarter-sawn, or flat-sawn and you'll have twodistinct different looks on the faces. when using a plunge router to make a mortiseit's always best to plunge a full-depth hole in the start and stop locations first, and this does a lot in preventing you from overshooting your start and stop points the further you go into the mortise.
now, actually removingthe material in between, i'm only making my cuts left to right from my eyes, and the reason being is the edge guideis on my side of the workpiece, so as the bit is spinningclockwise in the mortise, it's wanting to essentiallypull the router as it grabs, pull the router away from mybody and push it forward, due to the circular motion. so with the edge guide on my sideof the material, all that's going to do is keep the material or keep the edgeguide flush up against the material,
and keep it tracking perfectlyas i move left to right. so if i was to have the edge guideon my side and move right to left, the bit is still moving in a clockwise rotation and that will actually cause therouter to be pushed into me and the edge guide will no longer be referencedstopped up against the material. i would still hold it firmly in placebut it allows room for error, as the router will want to kind ofpush away from the mortise. the bit that i'm using isa one-half inch spiral up cut bit, and the up cut bit actually allowsthe material to be removed
a little bit easier inside themortise as it's being cut. but it is a one half of an inch diameter bit, and i find that this bit cuts the best in this particular router with the speedall the way down to its lowest setting. which in this case is 10,000 rpm. because the legs have so muchcharacter in them i chose the board that has the mostcharacter in it for the long rails, and for the short rails i chose a boardthat has just nothing but sapwood, that way, hopefully it'll tie thesapwood breadboard ends
of the table top in with the base. now the process for milling thisis pretty much the same, run through the thickness planerto skip planing both sides, join the edges, rip them to their finalsize at the table saw, and then cut them to theirfinal length at the miter saw. and at this point i can set up the dado stack inthe table saw to dial in the size for the tenons. i'm using one of the offcuts from wheni cut the long rails to their final length, that way i have the exact thickness material thati'm working with and it's just a scrap piece.
so i can use it to dial in theheight of the dado stack and that will give me the perfectwidth of the tenons for these rails. and once i have it dialed in, i can make all of my tenon cuts in the endof these rails without changing the setup. i intentionally made the mortise stoppedabout a half of an inch from the top of the leg and that is to provide a little bit morematerial support up here to prevent racking. so now i can cut this down to size and thenchop off the corners of the square tenons so that it'll fit into the rounded mortise. and after a few adjustments,back and forth at the bench,
the tenon should fit in therenice and snug. the tops are nice and flush, so this isone down, seven more for me to do. i'm using walnut as an accent wood on thistable and i want to make an inlay band all the way around the leg, so i've reduced the dado stack toabout a quarter of an inch in width and it's about one-eighth ofan inch depth for the cut and i'll make a band all the way around the baseof the legs about two inches up from the bottom. with a project like this it's gonna be alot easier to do as much surface prep as possible before assembly,
so i've already scraped all four of the apron railsas well as all four of the legs with a card scraper and now i'm ready for a rough assembly. i don't want to glue it together yet because i dowant to take measurements for the center support and i want to install that or fitthat before i glue it together. now these little walnut bandshere at the bottom, i was originally going to trim theseflush so they're just regular inlays, however i think i like thelook of them proud, so, last-minute design change, i guess,i'll leave these proud, and also the walnut band that i plan onadding to the bottom of the apron rails
later, i will make those proud justthe same amount as these are, i think it'll fit and adda nice little touch. but for right now i can doa dry assembly and get the measurement for the interior supportthat will connect both of the long rails. as you can see this pieceis not only a little bit short, it's not quite the sameheight as the side rails, that's because i just ripped it down on thetable saw, because i had to remove a defect that i didn't see previously. but it's also a quarter inchlong on either side,
and that is because i want toconnect it in the middle of the table to the long rails with aquarter-inch sliding dovetail. and the only purpose of this connectionin the middle of the table is to prevent these long rails from eitherbowing out, or coming in together over time. it'll just kind of tie everything together andoffer a little bit of support for the table top in the center of the table. to make the male end of the sliding dovetaili'll first use a marking gauge to establish where the dovetail will be, and then i'll use a chisel tomake a knife line for the saw,
the saw will cut the shouldersof the dovetail joint, and then i can just chisel therest of the shape as needed. to make the female end, or thepin side of the dovetail joint, it's just a matter of marking everythingout and then chopping away the waste. so this is the first sliding dovetailjoint i've done by hand, and not too bad, not great either. everything looks all right asfar as the geometry of it, but i went too far with my saw curve on oneside and add some chip out near the bottom. luckily, this is on the insideof the table, nobody will see it.
but i'll try to do better next time. so, the fit, is nice and tight, and it gets super tight at the end, so, i'm going to call that asuccess, thumbs up. one down, one to go andthen i can start assembly. i'm starting the assemblywith both of the short sides, and it's going to be easier to have these twoglued together before i add the long rails because i don't have any clamps big enoughfor the long rails to be connected.
i'm actually going to have to usea ratchet strap from my truck. but anyway, i want to make sure thati get all of the glue squeezed out off of the exterior of the joint onceit's glued together right now, rather than scraping it off later. as soon as this is done as being assembledi'm gonna go straight to a clear coat, a water-based polyurethane, and i don't want in to, i don't want to have to scrapeoff any glue at that stage. i am going to be using waterand a rag to pre-raise the grain,
and then lightly sand it downbefore i apply the finish, so i'm not concerned at all about getting a littlebit too much water on the surface of the project. as i clean the glue off of the joints. i'm adding these walnuts tripsto the bottom of the apron rails and these are sized the same as thewalnuts strips in the bottom of the legs. and this will kind of tie everything together. and they're going to be offset anoverhanging the bottom of the apron rails, the same amount as the overhangin the bottom of the leg. so these should complementeach other just fine.
also, the last thing i want to add during the glue-upis a couple glue blocks to each one of the corners. i think the mortise and tenon jointswill be really strong long-term but these added glue blockssure won't hurt anything. i left the base sit in clamps overnight to allowenough time for all the glue joints to properly dry and off camera i cut a smallchamfer on the bottom edge, of all of the legs and that's to prevent chip outif the table is dragged across the floor. and then also off camera i cut a bunchof slots on the inside of the top of the frame to allow for a tabletop hold down fastenersonce i need to assemble this in. so right now i've already taking it outsideit's a beautiful day, which is quite odd,
i was expecting rain today, but it's sunny, breezy and low humiditywhich is perfect for finishing. so, i've already raised the grain with somewater and sand it down all of the edges, or sand it down all the surfaces, blew off all the dust andi'm ready to apply a finish. i'm using water-based polyurethane for this, i've had great results withit for previous applications. so that's what i'm going with here, and, because of it is such a great day outside i thinki can get a couple coats on here relatively quick,
sanding with 220 grit sandpaper in between. and then i'll be ready forfinal assembly inside. as i've previously stated and also if you followme on social media or my second channel, you'll know that this project is gone throughso many different design changes. and i'm very very pleasedwith the final result, it's a simple table, but it has a little bit of extra touch hereand there with the walnut accents, which are simple in their own,they're just little strips of walnut, but i think they had a lot to the project.
and also, keeping the design very simple it allows the wood to do all thetalking rather than the design. and the hickory that wepicked out looks great. the legs that i was previously concerned with,with the insect damage, i'm extremely pleased i really likethe way that these turned out, the insect damage adds a little bit ofcharacter without being overwhelming. and then, also with the slab,as i was cutting it up, it was kind of a coin toss, because, in the slab state i could not seehow the wood grain would look,
and, now that i've had it all cut, plainedand then put some finish on it, it looks absolutely beautiful. i really really like this table. if you like a set of plans for thistable i do have them available, in this size as well as various othersizes that are larger than this. this is seated forfour people, which is the exact size that wewanted here in this house, we're just gonna have two benches, oneon either side, i'll build those at a later day, but for the size of this table,we wanted it this size because,
typically it's just me and my wife eating here,we don't have that much company eating over, and if we do have more than -say- four peopleto eat right here, then we do also have our breakfast bar and some foldingtables, which is very very rare. so, the main concern with me for making thetable this size, actually was for board games. me and my wife play a lot of board games, even while we eat diner we play "sorry!" justevery single night for the past five years, and, with this sized table, we can not only eat opposite of each otherwithout being in each other's way,
but we can also play our board gamesand reach to the other side, without having to really,really stretch over the table. anyway, thanks for watching, if you guys have any more questions onthis table, or the plans, or any of that stuff, there's a link in the description belowfor the website article for this project check that out, i'm sure most of the questionsare already answered there. thanks for watching, you guys take care, and have a great day.
0 Response to "modern rustic dining room"
Post a Comment