parsons dining room chairs
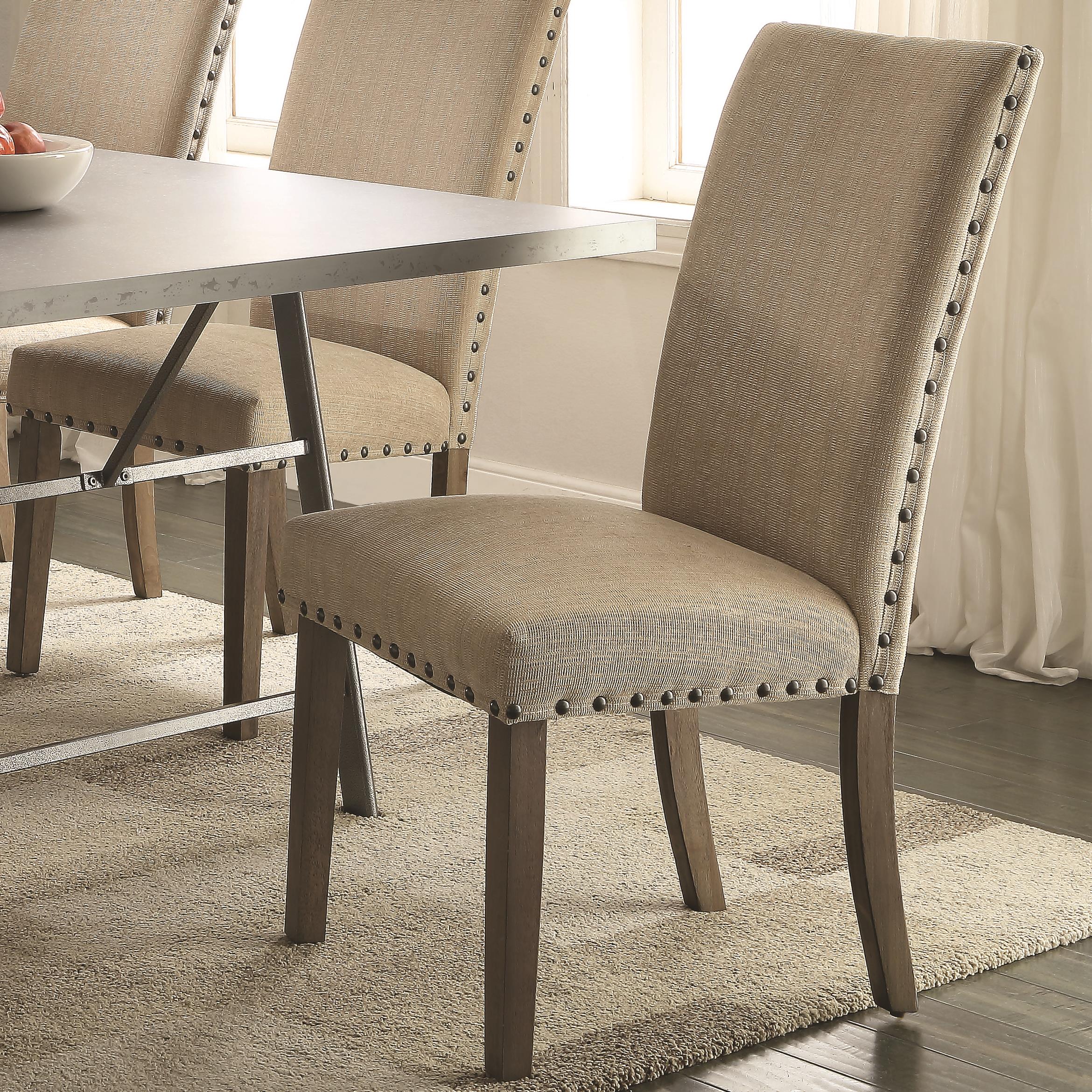
this week on johnny build i built a modern style farmhouse table a parsons table to be more accurate a parsons table features legs pushed all the way out to the ends and flush with the top and was designed almost a hundred years ago to be a basic lasting design whether left unfinished she then gold or in this case inlaid epoxy and reclaimed wood this table is built from a mixture of red and white barn wood oak that is likely 50 to 100 years old my friends at vintage reclaimed lumber in oklahoma city provided all the wood for this project and they are the sponsors of this video more on vrl later and down in the description below as i pick out my boards you can see the issues working with wood like this
none of these boards were straight and many of them were cupped or twisted for being such a simple design this was one of the most challenging projects i've ever completed every step along the way was a learning experience and i had a few setbacks along the way the legs are made from this reclaimed beam. that was almost 15 feet long we brought the beam into the vrl shop to mill the legs and the first step was to cut them down to 32 inch long sections the beam was about 11 to 12 inches wide in about five and a half inches tall and as you see i had to flip the beam over and make this cut in two passes using this giant medieval tanna whit's bandsaw. i resaw the leg blanks in half and this is where i
encountered my first hiccup. the blade was deflecting and preventing me from getting straight cuts now i managed to get the leg blanks greased on on the bandsaw but that left a lot of cleanup work to be done to get them squared up next i ran the leg blanks through the jointer to get to flat and square surfaces then i had to use this 14-inch ripp blade to cut the legs to their final width a four and a quarter inches square back in my own shop i laid out all the boards for the table top and measured out how much usable material i had in each one i ended up with an alternating pattern of red and white oak boards for the tabletop and then i could cut these boards down to a rough length of 90 inches long
this table is gonna be 7 feet long and this gives me a bit of wiggle room before cutting the tabletop to its final length i ran all these boards to my jointer to get a flat edge and then i cut them down to their final width of 5 inches over on the table saw i started with the 5 boards that will make up the longer middle portion of the table and i'm using dominoes to help with the alignment since the boards are a little bit warped probably more than i needed but it helped pull these boards back into alignment i added dominoes and glue to put these two boards together now as a bit of a task to get these two boards to line up
but with a little bit of coaxing and a good wooden mallet i was able to make it work once the glue a draw i took the boards out of the clamps and i use my stanley number 5 jack plane to smooth at the bottom and then i skip playing the boards to help flatten the top without losing too much of that character of the wood. i repeated this process for the remaining boards and then glued up all 5 planks that make up the long section of the tabletop again using dominoes for alignment and to help pull everything together as straight as i could get it with a bit more coaxing i got the whole top in the clamps and added some call boards wrapped and packing tape to the end to prevent further bowing once the top had dried i flipped it over on my workbench and shimmed up the high spots now the idea here is to use a router sled to flatten the bottom as much as possible
then i could flip the whole thing over and hit the top of the table only removing the high spots and leaving all the character with the longer section of the tabletop done now i could add the two shorter boards to the ends that the legs will sit flush against i sanded them down and use the legs to mark the exact width. they need to be and then rip them over on my table saw clamp the legs flush with the end of the table and use the leg on the other end to mark their length which i cut over on the miter saw i had a domino's to these boards and attach them to the longer portion of the table with some glue and a little bit of brute force clamping pressure to pull everything into alignment i
came back with my jack plane and also this little block plane to flush up this board and the seam to the rest of the tabletop moving on to the legs the next step was to hit them with a belt sander and an 80 grit belt to remove most of the grit built up over the last 60 or so years once that was done it was time to start pouring the epoxy inlays i started with the tabletop and i used aluminum tape here to short the bottom of the table first this is my first time to use this east coast resin and i had really good results i mixed equal parts resin and hardener and made sure it was thoroughly mixed before i added the blue green and white pearl pigments to get the depth of color i was going for
and now it was time to pour as you can see here my first pour in the tabletop was a bit sloppy and the uneven surface caused it to spread out a little bit i got a bit more efficient with my pours, but i still had a lot of overflow that i had to address later i also mixed some sawdust into a batch of epoxy and filled any of the small gaps with boards connected the legs had several large cracks that i decided to backfill with this bondo fiberglass. resin it's much cheaper than the two-part epoxy i was using but in hindsight, i think i would have been better off just filling everything with the same pigmented resin this caused some issues of having the chip away some of this resin that was showing through the pigmented resin later on and
once at a draw i came back with the coloured epoxy and filled it in over the bondo. resin i wanted to leave some of the checks for aesthetic reasons but some of the bigger cracks had to be addressed for stability also a quick tip don't use regular packing tape like i did here. it did not contain the epoxy well at all i quickly switched back. so using the aluminum tape also these epoxy pours actually took several weeks to complete i had multiple surfaces to fill and often i would come back after the epoxy dried to find that it just flowed down into some unseen crack after pouring the epoxy i used the heat gun to pop any air bubbles and then i came back to remove the over-pour with a chisel after it dried i also sanded down the resin and it was here that i realized the sanding was heating up the resin and making it easier to
chisel away i tried using a heat gun, and this worked great this made my epoxy over pore removal go much faster and have a much cleaner result. i repeated this whole process all over again on the knots and cracks in the wood that i used for the aprons and once all these numerous epoxy pores were done i sanded the resin first was 600 grit sandpaper then 1200 grit and finally 2,000 grit to get the shine that i was looking for now to begin assembling the tables and this is where i ran into a lot of issues i use the sheet of plywood on the flattest portion of my shop to have a good surface of reference to fit at the legs i clamp the legs in place added a few weights to keep the table from bowing up and then mark the alignment of the legs the aprons were cut oversized and i use this setup to mark out their exact length of roughly
25 inches i cut them to fit on the miter saw and then repeated this process for the other three aprons. i came up with these 45-degree rest and a drilling jig the mortise had a slot for diagonal braces to hold the legs of the apron and spoiler it did not work at all the idea was that shizz allowed these mortises. where a 45 degree angle that was going to hold the aprons could rest up against the leg and then i would drill a lag bolt in through the leg to secure everything having the legs held on only by a single bolt made them far too wobbly and i had to remake the whole entire apron structure because i had already glued the battens in place
so back to the drawing board, i had to make all new aprons and rethink their connection to the legs again i cut them to fit against the legs. but this time i marked out with the apron made it up to the legs. i cut in two dominoes to the end of each apron and matching domino's on the legs themselves now i could dry fit the aprons and add the sinner stretcher and battens seen here also using domino's i took the whole apron assembly apart and then reassembled it piece by piece this time adding glue the way i clamped up the table base without the tabletop in place cause some major issues. i'll explain more in a bit but first you see me putting the tabletop in place and then marking out where i need to cut it flush with the legs which i then did with my tracks off i added some dominoes to the aprons that are going to allow me to attach the table top with some tabletop buttons and
finally, i can move on to the finish. i use this general finish's satin water-based topcoat it's my first time to ever use this finish and i'm very pleased with the results. i put four coats on put in all the tabletop buttons and attached the tabletop and that's when i discovered some issues with the fit when i clamped up the apron structure to the legs the uneven clamping pressure and the fact that none of the reclaimed wood is perfectly straight managed to pull the base out of alignment and this left me with these gaps and this table just did not meet my standards this whole time i was building a second table in the background i learned from those mistakes in the first table fix them on the second table, and i couldn't be more pleased with the results. i want to give a special thanks to the sponsor of this video vintage reclaimed lumber if you're in the oklahoma city area, make sure to check them out
they've got a great selection of reclaimed lumber beautiful live-edge slabs and old timber beams. if you're not in the oklahoma city area check them out online at be our lumber calm they do ship anywhere in the country just use the code johnny 10 for 10% off of your order as always thank you so much for watching let me know what you think down in the comments below if you liked it, make sure to hit that thumbs up and please subscribe thanks for checking this one out and we'll see you back here next time
0 Response to "parsons dining room chairs"
Post a Comment